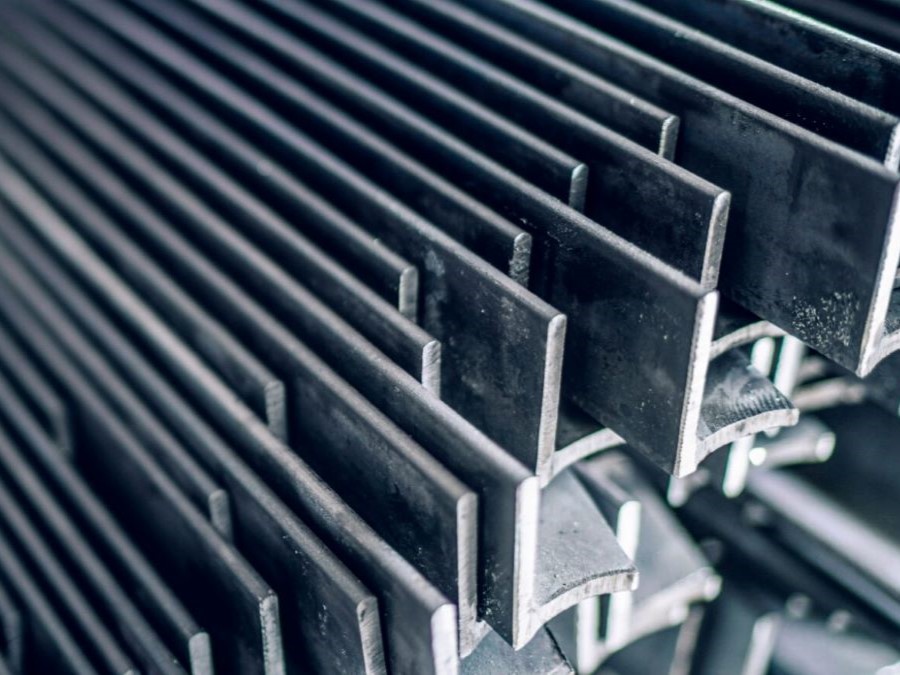
Ekstrüzyon, bir malzemenin belirli bir kesite sahip bir profil şeklinde dışarı itilerek şekil alma işlemine ve sürecine denir. Ekstrüzyon işlemi, genellikle termoplastikler, elastomerler, seramikler ve bazı metallerin işlenmesinde kullanılır. Ekstrüzyon süreci sırasında malzeme, ısıtıldığı veya eritildiği bir silindir içinden geçirilir. Daha sonra bu malzeme yüksek bir basınç altında belirli bir şekli olan bir nozul veya kalıptan geçirilir. Malzeme kalıptan çıktığında, belirli bir kesit profiline sahip uzun ürün elde edilir. Bu ürün, genellikle tüpler, çubuklar, levhalar veya film şeritleri şeklinde olabilir.
Ekstrüzyon Ne İçin Kullanılır?
Ekstrüzyon, sabit bir kesite sahip metal nesneler yapmak için kullanılır. Bu, onların belirli bir açıda kesilmesi gerektiği anlamına gelir. Ekstrüzyon genellikle ekstrüde edilen metali eriterek daha yüksek sıcaklıklarda gerçekleştirilir. Bu, süreci çok yönlü kılar, çünkü bu şekilde daha kırılgan metallerle çalışabilir.
Ekstrüzyon Türleri Nelerdir?
Ekstrüzyon birçok endüstride farklı ihtiyaçlara yanıt olarak kullanılmaktadır. Ekstrüzyon türlerinin ana hatlarıyla belirlenmesi, kullanılan malzemenin, uygulamanın ve ekipmanın özelliklerine göre değişkenlik gösterebilir. İşte en yaygın kullanılan ekstrüzyon türleri :
Sıcak ekstrüzyon
Sıcak ekstrüzyon, bir malzemenin yüksek sıcaklıklarda ekstrüde edildiği bir işlem metodudur. İşlem sırasında, malzeme ekstrüzyon sıcaklığına ısıtılır, bu da onun yumuşak bir hale gelmesine neden olur. Daha sonra bu ısıtılmış malzeme, belirli bir şekil veya kesite sahip bir ürün oluşturmak için bir matris veya ölçer üzerinden yüksek bir basınçla itilir. Sıcak ekstrüzyon, çelik, alüminyum, bakır, pirinç, titanyum ve birçok diğer metalde yaygın olarak kullanılır. Sıcak ekstrüzyon prosesi, istenilen ürünün şekli, boyutu ve kullanılan malzemeye bağlı olarak değişiklik gösterebilir.
Sıcak ekstrüzyonun özellikleri ve avantajları şunlardır: • Daha İyi Şekillendirme: Yüksek sıcaklık, birçok metalin ve diğer malzemelerin daha kolay şekillendirilmesini sağlar. • Daha geniş Malzeme Yelpazesi: Daha sert ve kırılgan malzemeler bile sıcak ekstrüzyon ile şekillendirilebilir. • Daha İyi Yüzey Kalitesi: Sıcak ekstrüzyon, malzemelerin daha düzgün bir yüzey kalitesiyle ekstrüde edilmesini sağlayabilir. • Mikroyapı Değişiklikleri: Sıcak ekstrüzyon, malzemenin mikro yapısında değişikliklere neden olabilir, bu da mekanik özelliklerini etkileyebilir.
Soğuk ekstrüzyon
Soğuk ekstrüzyon, malzemenin oda sıcaklığında veya sadece hafifçe ısıtılarak belirli bir şekil veya kesite sahip bir ürün oluşturmak için bir matris veya ölçer üzerinden yüksek bir basınçla itilmesi işlemidir. Soğuk ekstrüzyon, malzemenin deformasyonunu teşvik eder, bu da malzemenin yeniden kristalleşmesini engeller. Soğuk ekstrüzyon, özellikle çelik, alüminyum ve bakır gibi metallerin işlenmesinde yaygın olarak kullanılır. Ancak, malzemenin sertliği ve kırılganlığı, ekstrüzyon sürecinin ne kadar etkili olacağını belirleyebilir.
Soğuk ekstrüzyonun özellikleri ve avantajları şunlardır: • Yüksek Mekanik Özellikler: • Tane Yapısındaki Değişiklik: Soğuk ekstrüzyon işlemi sırasında metalin tane yapısı sıkıştırılır. Bu, malzemede mikroskobik seviyede bir dizi değişikliğe yol açar, bu değişiklikler malzemenin mukavemetini ve sertliğini artırır. • Dayanıklılık: Soğuk işlem görmüş metaller, tane sınırlarının sıkışması nedeniyle orijinal, işlenmemiş hallerine göre daha yüksek bir yorulma dayanımına sahiptir. • Daha İyi Yüzey Kalitesi: • Düzgün Yüzey: Soğuk ekstrüzyonla üretilen ürünler, parlak ve düzgün bir yüzeye sahip olabilir. Bu da sonraki işlemlerde, örneğin kaplama veya boyama için ideal bir yüzey oluşturur. • Oksidasyonun Önlenmesi: Isıtma işlemi olmadığı için oksidasyon oluşumu minimalize edilir, bu da metallerin yüzeyinde kusurların oluşmasını engeller. • Tolerans ve Boyutsal Hassasiyet: • Hassas Üretim: Soğuk ekstrüzyon işleminde yüksek basınçlar kullanılır, bu sayede üretilen parçaların boyutsal toleransları oldukça dar bir aralıktadır. • Kalite Kontrolü: Üretim sürecinde daha az değişken olduğundan, süreç üzerinde daha iyi bir kontrol sağlanır, bu da boyutsal hataların minimize edilmesine olanak tanır. • Daha Az Atık: • Verimli Malzeme Kullanımı: Soğuk ekstrüzyon, malzemeyi daha etkin bir şekilde kullanır, bu da daha az hammadde kullanımı anlamına gelir. • Çevresel Avantajlar: Atık azaldığı için çevresel etkisi de azalır, bu da sürdürülebilir üretim yöntemlerine uygun bir yaklaşımdır. • Ek Isıl İşlem Gereksinimi Yok: • Mikro Yapıda İyileştirme: Soğuk ekstrüzyon, malzemenin mikroyapısını iyileştirir, bu da çoğu durumda ek ısıl işlemlerin gereksiz hale gelmesine neden olur. • Üretim Hızı: Ek işlem gereksinimlerinin ortadan kalkması, üretim süreçlerini hızlandırır ve toplam üretim maliyetini düşürür. • Enerji Tasarrufu: Isıtma Gereksinimi Olmaması: Soğuk ekstrüzyon sürecinin ısıl enerji gereksinimi olmadığı için enerji tüketimi azalır. Maliyet Etkinliği: Enerji maliyetlerini azaltarak, genel üretim maliyetlerini de optimize eder.
Doğrudan Ekstrüzyon
Doğrudan ekstrüzyon, malzemenin bir matris veya kalıp üzerinden doğru bir şekilde itildiği bir ekstrüzyon tekniğidir. Doğrudan Ekstrüzyon aynı zamanda "ileri ekstrüzyon" olarak da bilinir. Doğrudan ekstrüzyonun işleyişi, bir silindirin içine yerleştirilen metal kütlesi veya billet bir piston ya da itici tarafından yüksek bir basınçla itilir. Piston, malzemeyi bir kalıp veya matrisin deliğinden geçirerek malzemenin istenen kesit şeklini almasını sağlar. Bu ekstrüzyon işlemi sırasında, matris hareketsiz kalırken, malzeme doğru bir şekilde ileriye doğru itilir. Bu, malzemenin ve pistonun aynı yönde hareket ettiği için "doğrudan" veya "ileri" ekstrüzyon olarak adlandırılır.
Bu yöntemin avantajları arasında ekipmanın daha basit ve dolayısıyla daha ekonomik olması sayılabilir. Ancak, sürtünme nedeniyle ekstrüde edilen malzemenin itici ile arasında daha fazla ısı üretimi olabilir. Bu nedenle, bazen soğutma veya yağlama yöntemleri kullanılarak bu ısıyı kontrol altında tutmak gerekebilir.
Dolaylı Ekstrüzyon
Dolaylı ekstrüzyon, ekstrüzyon sürecinin bir varyasyonudur ve genellikle "ters ekstrüzyon" olarak da adlandırılır. Bu yöntemde, itici veya piston hareket ederken matris de hareket eder, ancak malzeme (genellikle bir metal kütlesi veya billet) hareketsiz kalır. Matris, malzemenin etrafına yerleştirilir ve itici, matrisi malzemenin üzerine doğru itmek için kullanılır. Bu, matrisin malzemeyi şekillendirerek istenen kesit şeklini oluşturmasını sağlar. Yani aslında matris malzemenin içine doğru hareket eder.
Dolaylı ekstrüzyonun özellikleri ve avantajları şunlardır: • Daha Az Sürtünme: Dolaylı ekstrüzyonda, malzeme ile kalıp arasında sürtünme daha azdır. Bu, malzemenin kalıp içerisinde daha düzgün bir şekilde hareket etmesine olanak tanır. Doğrudan ekstrüzyonda, malzeme kalıp boyunca sürekli olarak sürtünerek hareket ederken, dolaylı ekstrüzyonda bu sürtünme minimuma indirilir. Daha az sürtünmenin olması, malzemenin daha homojen bir şekilde ekstrüde edilmesini sağlar ve ayrıca takım ömrünü uzatır. • Daha Uzun Parçalar: Dolaylı ekstrüzyon, daha uzun parçaların üretimine olanak tanır. Malzemenin hareket yönüne zıt bir yönde hareket etmesi nedeniyle, ekstrüzyon sırasında malzemenin daha uzun mesafelerde deformasyonu mümkündür. Bu özellik, özellikle belirli endüstriyel uygulamalar için avantajlıdır, çünkü daha uzun bileşenler veya ürünler talep edebilir. • Daha İyi Yüzey Kalitesi: Daha az sürtünme, malzemenin kalıp yüzeyiyle daha az temas etmesi anlamına gelir. Bu, ekstrüde edilen ürünün daha düzgün ve pürüzsüz bir yüzeye sahip olmasını sağlar. Daha iyi yüzey kalitesi, son ürünün estetik açıdan daha çekici olmasının yanı sıra, bazı uygulamalar için (örneğin, hassas mühendislik parçaları) fonksiyonel avantajlar da sağlar. Pürüzsüz yüzeyler, malzemenin korozyona veya aşınmaya karşı daha dirençli olmasına yardımcı olabilir.